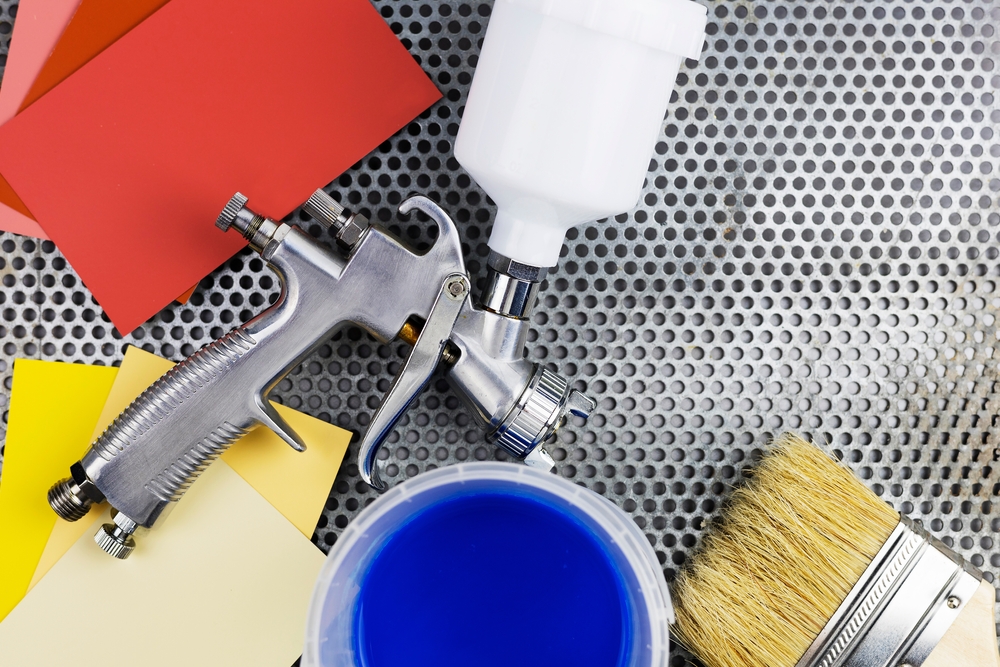
Ensuring Safety: How to Maintain Your Paint Booth Fire Suppression System
August 7, 2024 5:55 pm Leave your thoughtsIn industries where paint booths are used, maintaining a robust fire suppression system is crucial. Paint booths, often filled with flammable materials and solvents, pose a significant fire risk. Ensuring the reliability of your fire protection system not only safeguards your facility but also ensures compliance with safety regulations. In this blog, we’ll explore the essential aspects of maintaining fire protection systems in paint booths, covering everything from routine inspections to system upgrades.
The Importance of Fire Protection in Paint Booths
Understanding the Risks
Paint booths are designed to handle flammable materials safely, but their very nature makes them susceptible to fire hazards. The combination of volatile organic compounds (VOCs), solvents, and potentially high temperatures creates an environment where even a small spark can lead to a catastrophic fire. Hence, a well-maintained fire suppression system is a vital component of a paint booth’s safety measures.
Regulatory Compliance
Ensuring that your paint booth fire suppression system is properly maintained is not just about safety; it’s also about compliance. Regulatory bodies such as the National Fire Protection Association (NFPA) and local fire codes have stringent requirements for fire protection systems. Regular maintenance ensures that you meet these standards and avoid potential fines or penalties.
Key Components of Paint Booth Fire Suppression Systems
Fire Detection Systems
Fire detection systems are the first line of defense. They detect heat or smoke and trigger the suppression system. Components such as smoke detectors, heat sensors, and flame detectors must be regularly tested to ensure they function correctly.
Fire Suppression Agents
Different types of fire suppression agents are used, including water-based systems, dry chemical agents, and foam systems. Each has its own maintenance requirements. For example, dry chemical agents need periodic refilling and checking of discharge nozzles.
Control Panels
The control panel acts as the brain of the fire suppression system, managing alarms, notifications, and activation of the suppression agents. Regular checks are essential to ensure that it responds accurately to potential fire threats.
How to Maintain Fire Protection Systems in Paint Booths
Routine Inspections
Routine inspections are critical to ensure that all components of the fire suppression system are functioning correctly. Here’s what to look for:
- Visual Checks: Inspect fire alarms, sensors, and nozzles for any visible signs of damage or obstruction.
- Functional Tests: Test detectors and alarms to confirm they are operational. Simulate alarm conditions to ensure the system responds as expected.
- Agent Levels: Check the levels of suppression agents to ensure they are at the recommended levels.
Cleaning and Upkeep
Keeping your fire suppression system clean is essential for its efficiency. Dust, debris, and paint overspray can interfere with sensors and nozzles. Regular cleaning schedules should be established to prevent buildup.
- Sensor Cleaning: Gently clean smoke detectors and heat sensors to remove dust or contaminants.
- Nozzle Maintenance: Ensure that fire suppression nozzles are not clogged. Clean them regularly and replace any damaged nozzles.
Professional Maintenance
While routine checks can be handled in-house, professional maintenance is necessary to ensure thorough inspections and servicing. Certified fire protection professionals can provide detailed checks and repairs that may not be evident during routine inspections.
- Annual Inspections: Schedule annual inspections with a certified technician to ensure compliance with safety standards.
- System Upgrades: Professionals can recommend and install system upgrades as needed, such as updated detection technologies or more efficient suppression agents.
Documentation and Record-Keeping
Proper documentation is crucial for both compliance and operational efficiency. Maintain detailed records of all inspections, maintenance activities, and any repairs made to the fire suppression system.
- Inspection Logs: Keep logs of routine inspections, including dates and findings.
- Maintenance Records: Document all professional maintenance and upgrades performed on the system.
- Compliance Reports: Store any reports or certificates related to regulatory compliance for easy access during audits.
Troubleshooting Common Issues
False Alarms
False alarms can be disruptive and lead to unnecessary downtime. Common causes include dust buildup or malfunctioning sensors. Regular maintenance and cleaning can help reduce the occurrence of false alarms.
System Failures
If the fire suppression system fails to activate during an emergency, it could be due to various issues such as depleted suppression agents, faulty sensors, or a malfunctioning control panel. Immediate professional evaluation is necessary to identify and resolve such issues.
Inadequate Coverage
Ensure that your fire suppression system covers all areas of the paint booth effectively. Inadequate coverage can leave parts of your facility unprotected. Regular reviews of your system’s layout and coverage areas can help address any deficiencies.
Upgrading Your Fire Suppression System
Emerging Technologies
Advancements in fire suppression technology offer improved safety features and efficiency. Explore new technologies such as advanced detection systems, automated suppression controls, and more effective suppression agents.
Retrofitting
Retrofitting your existing system with new components or technologies can enhance its effectiveness. Consult with fire protection professionals to determine the best retrofit options for your paint booth.
Compliance Updates
Regulations and standards evolve over time. Regularly review and update your fire suppression system to ensure it meets the latest safety codes and regulations.
Conclusion
Maintaining your paint booth fire suppression system is a continuous process that requires diligence and expertise. By adhering to routine inspections, professional maintenance, and staying informed about technological advancements, you can ensure the safety of your facility and compliance with regulatory standards. Remember, a well-maintained fire protection system not only prevents catastrophic events but also supports the smooth operation of your paint booth.
Need Fire Protection Systems in Longview, TX?
Welcome to Anchor Safety Inc.: the premier fire protection system and equipment provider of Longview, TX. Anchor Safety Inc. specializes in consultation, service, sales, and installation for fire protection systems for homes, offices, restaurants, computer server rooms, and document rooms. We carry and service all major brands, including Amerex, Ansul and Kidde. Anchor Safety Inc. is a member of FEDOT and the NAFED, as well as the Longview Chamber of Commerce. In business since 1990 with over 50 years of industry experience under our belts, you can trust in our expertise when it comes to fire safety. Give us a call for a free estimate or consultation for your fire safety.
Categorised in: Paint Booth Fire Protection
This post was written by admin